Capacity Cost
Categories: Econ, Company Management
Many manufacturing companies experience the nice problem of not having enough capacity to handle all the customer orders that keep pouring in. They might need to expand the factory, add new equipment or hire more people, all of which are considered to be capacity costs.
Some are temporary costs such as leased space, contract workers, adding an extra shift or renting equipment that can be eliminated if demand decreases again. But some capacity costs are more permanent, such as an extension on a building or a new automated production line.
So, when You Name It, We Build It Inc. receives a big order from a Chinese company, they do a careful analysis of what extra capacity costs they are willing to incur: extra workers, extra shifts with increased heating or air conditioning, rented equipment, leased space, etc. Since the customer might copy everything and never place a big order again, We Build It decides to make most of the extra capacity costs temporary in nature.
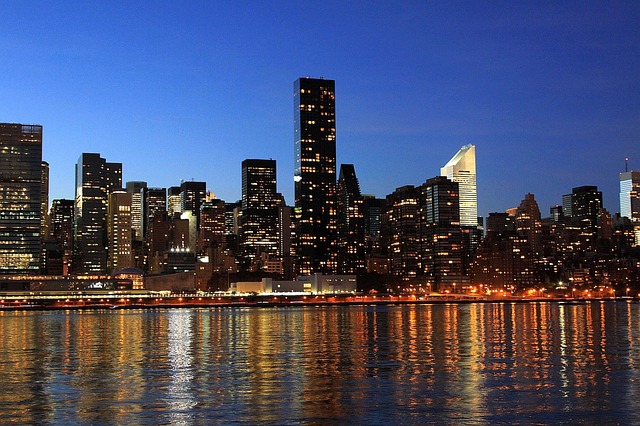